Understanding GRP Electrical Enclosures: A Comprehensive Guide
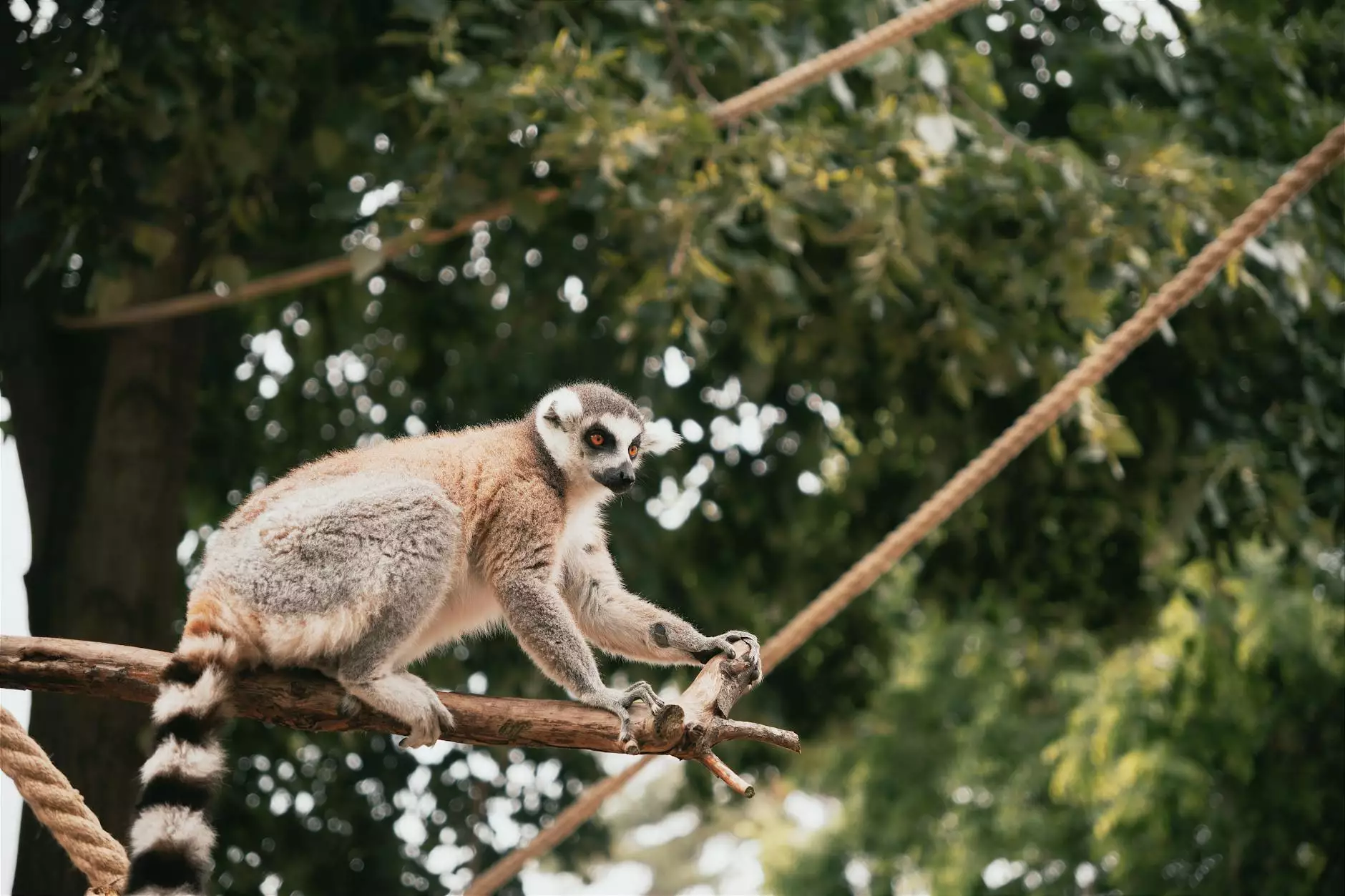
The world of electrical installations and safety equipment is vast and complex, yet it is fundamental to all modern infrastructure. Within this realm, GRP electrical enclosures (Glass Reinforced Plastic) have become increasingly popular due to their exceptional properties. This article aims to dive deep into what GRP electrical enclosures are, their numerous benefits, applications across various industries, and why they are often the best choice for safeguarding electrical components.
What are GRP Electrical Enclosures?
GRP electrical enclosures are protective casings made from a composite material – primarily glass fibers and resin. They are designed to house electrical equipment and safeguard it from external environmental factors, which is crucial for maintaining operational integrity and safety. The glass fibers provide strength, while the resin offers excellent resistance to corrosion and environmental stressors.
The Benefits of Using GRP Electrical Enclosures
Choosing the right enclosure for electrical components is vital for safety and performance. The benefits of GRP electrical enclosures are numerous:
- Corrosion Resistance: GRP enclosures are inherently resistant to many harsh chemicals and environmental factors, making them ideal for use in chemical plants, offshore installations, and coastal locations.
- Lightweight: Compared to metal enclosures, GRP enclosures are significantly lighter, which simplifies installation and reduces transportation costs.
- Durability: The robust construction of GRP ensures that these enclosures can withstand impact and physical stress, making them suitable for harsh environments.
- Electrical Insulation: GRP offers excellent electrical insulation properties, reducing the risk of electrical faults and ensuring user safety.
- Design Flexibility: GRP enclosures can be molded into various shapes and sizes, allowing for custom solutions that meet specific project requirements.
- UV Resilience: GRP enclosures can be formulated to withstand UV radiation, ensuring longevity in outdoor applications.
- Low Maintenance: Unlike metal enclosures that may require regular painting or treatment to prevent rust, GRP enclosures require minimal upkeep.
Applications of GRP Electrical Enclosures
GRP electrical enclosures are versatile and find usage in a broad range of industries, including:
1. Telecommunications
In the telecommunications sector, these enclosures protect essential equipment from weather elements and vandalism, thus ensuring uninterrupted service.
2. Renewable Energy
With the growth of solar and wind energy, GRP enclosures are widely used in housing inverters, batteries, and control equipment, providing robust protection in outdoor installations.
3. Oil and Gas Industry
The oil and gas sector often operates in challenging environments. The chemical resistance properties of GRP make it suitable for protecting electrical systems in refineries, offshore rigs, and pipelines.
4. Water Treatment Plants
Water treatment involves various chemicals; hence, GRP enclosures are invaluable for housing control panels and instrumentation, ensuring they remain intact and functional.
5. Industrial Manufacturing
In manufacturing settings, GRP is used to protect sensitive electrical distribution and automation components from dust, moisture, and mechanical damage.
Key Considerations When Selecting GRP Electrical Enclosures
When choosing GRP electrical enclosures, several factors should be considered:
- Environmental Conditions: Assess the environment in which the enclosure will be placed, including exposure to chemicals, temperature extremes, and physical impacts.
- Size and Design: Determine the size of the equipment and the necessary space for ventilation and maintenance access.
- Ingress Protection (IP) Rating: Ensure that the enclosure has an appropriate IP rating to prevent dust and water ingress.
- Standard Compliance: Verify that the enclosure meets relevant industry standards such as BS EN 60529 for IP ratings and other safety standards.
- Customization Options: Some projects may require specific modifications; inquire if the manufacturer can tailor enclosures to your needs.
Installing GRP Electrical Enclosures
Proper installation of GRP electrical enclosures is crucial to ensure their effectiveness. Key steps in the installation process include:
1. Site Preparation
Prepare the site by ensuring a level foundation that can support the weight of the enclosure. Consider any height requirements for accessibility.
2. Mounting the Enclosure
Follow the manufacturer's guidelines for mounting. Most GRP enclosures can be bolted to a base or wall-mounted depending on the application.
3. Electrical Connections
Ensure all wiring is done safely and in accordance with relevant electrical codes. Properly sealing cable entries can prevent water ingress.
4. Sealing and Maintenance
Post-installation, ensure that all seals are intact, and perform routine maintenance checks to verify the integrity and functionality of the enclosure.
Conclusion
In summary, GRP electrical enclosures represent a cornerstone of safety and reliability in electrical systems across various sectors. Their unique combination of strength, durability, and resistance to environmental factors makes them a superior choice for protecting sensitive electrical components. Whether in telecommunications, oil and gas, renewable energy, or industrial applications, the selection of GRP enclosures not only enhances safety but also contributes to the longevity and efficiency of electrical systems. As sustainability and safety become ever more critical in industrial design, the demand for innovative solutions like GRP will undoubtedly continue to rise.
For more information on how Celtic Composites can provide tailored GRP electrical enclosure solutions to meet your specific needs, visit celticcomposites.co.uk.